This is an important message for University organizations that store valuable materials in temperature-controlled units (units). You are responsible for forwarding this information to applicable researchers and staff, as well as for following up as appropriate.
University researchers suffer losses of high value research material due to malfunctioning units every year. It is extremely time consuming and difficult for researchers to fully document the specific items lost and justify claimed values, and in many cases, the materials cannot all be recreated. Insurance recoveries have amounted to a small fraction of the researcher’s estimates, and there is always a possibility that insurance coverage may become more limited and/or may be cancelled in future years.
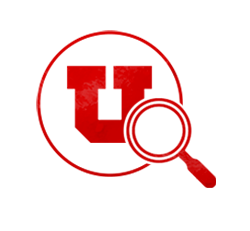

To ensure that units are maintained to work their best, University administration has made PMAs a requirement for all units covered by insurance. Arrange to have all units inspected, and preventative maintenance done at least on an annual basis. In the event of a loss, evidence of a PMA that was in effect at the time of the loss will be required in order to process an insurance claim.
The University no longer has a preferred PMA vendor under contract. Please follow University protocol in your hiring of a third-party vendor. You may also consider working with the manufacturer of your cooling unit to see if they service or recommend a vendor to provide preventative maintenance. Make sure to have a member of your department present during the preventative maintenance to answer questions and be a witness to the work being performed.
Your facility manager may provide recommendations for vendors.
I hope you find this information helpful in your efforts to protect your valuable materials stored in your temperature-controlled units. If you have further questions about this new PMA requirement, please contact the Office of the Vice President for Research. If your questions relate to insurance specifically, please email University Risk & Insurance Services.
Points of Clarification
CONTACT INFORMATION FOR YOUR FREEZER
Please provide full contact information on the front of your freezer or temperature-controlled room for people who can assist facilities personnel in assessing freezer contents in the event of an emergency freezer failure.
Forms for doing this can be found at cores.utah.edu under the ‘Freezer’ Tab.
Preventive Maintenance Agreements (PMA’s) Required
for Temperature Controlled Units
- Informal understandings or verbal agreements are not acceptable. PMAs must be in writing.
- Staff from the department that owns or operates the cooling unit may not conduct preventive Maintenance.
- Acceptable PMA providers include:
- Any outside (non-U) vendor (per procurement guidelines, the total annual payments to any one vendor by a U department may not exceed $10,000)
- A cooling unit manufacturer under a preventive maintenance plan or recommended vendor suggested by them.
- Hospital Facilities & Engineering (Brandon Wall ext. 1-2781, Ismael (Junior) Marrero ext. 1-3290).
- Annual Preventive Maintenance consists of...
- Comply with all manufacturer’s recommendations
- Inspect, test and change the batteries in the continuous monitoring alarm system unit
- Inspect electrical connections
- Inspect and clean the door gaskets
- Inspect refrigeration systems
- Inspect controls for proper operation
- Temperature check and calibration
- Place a sticker on the unit with the date the PM service was performed
- Written report on each unit
- Assurance that the freezer is operating normally (temperatures within range, no abnormal noises or frost buildup, etc.)
- Assessment of door seal / gaskets and hinge & latching mechanisms
- Assessment of minimum clearances around the exterior of the equipment as specified by the manufacturer (to ensure adequate airflow)
- Certification of the status of any air filters
- Certification that the coils, ventilation grills are clean and free from damage
- Certification that fan blades (where present) are clean, free from damage and operate properly
- Certification that the battery meets functional testing
- Assessment of the frost situation (interior)
- Assurance that the thermostat is calibrated
- Assessment of electrical connection (frayed or loose wiring, use of extension cords, etc.)
- For freezers with LN2/CO2 backup systems, assurance that the backup system is functional
- A representative of your department must accompany the PMA provider during the annual onsite PMA inspection.
If you have further questions about this PMA requirement, please contact the Office of the Vice President for Research. If your questions relate to insurance specifically, please email University Risk & Insurance Services.